The Best Strategy To Use For Alcast Company
The Best Strategy To Use For Alcast Company
Blog Article
Unknown Facts About Alcast Company
Table of ContentsGetting The Alcast Company To WorkAlcast Company for BeginnersSome Known Incorrect Statements About Alcast Company Our Alcast Company DiariesAlcast Company for BeginnersNot known Facts About Alcast Company
The refined difference hinges on the chemical material. Chemical Comparison of Cast Aluminum Alloys Silicon advertises castability by decreasing the alloy's melting temperature and improving fluidness during spreading. It plays a vital role in enabling elaborate mold and mildews to be loaded accurately. Additionally, silicon adds to the alloy's toughness and wear resistance, making it valuable in applications where toughness is important, such as automotive components and engine elements.It also enhances the machinability of the alloy, making it easier to refine right into ended up products. By doing this, iron adds to the general workability of aluminum alloys. Copper enhances electrical conductivity, making it helpful in electric applications. It likewise improves deterioration resistance and contributes to the alloy's overall toughness.
Manganese adds to the toughness of aluminum alloys and boosts workability (Aluminum Castings). It is typically utilized in functioned aluminum items like sheets, extrusions, and profiles. The presence of manganese help in the alloy's formability and resistance to breaking during fabrication procedures. Magnesium is a light-weight component that offers strength and impact resistance to aluminum alloys.
Alcast Company Can Be Fun For Everyone
It enables the production of light-weight parts with exceptional mechanical residential or commercial properties. Zinc improves the castability of light weight aluminum alloys and helps regulate the solidification process during spreading. It enhances the alloy's toughness and firmness. It is commonly located in applications where intricate shapes and great details are required, such as decorative spreadings and certain automotive components.
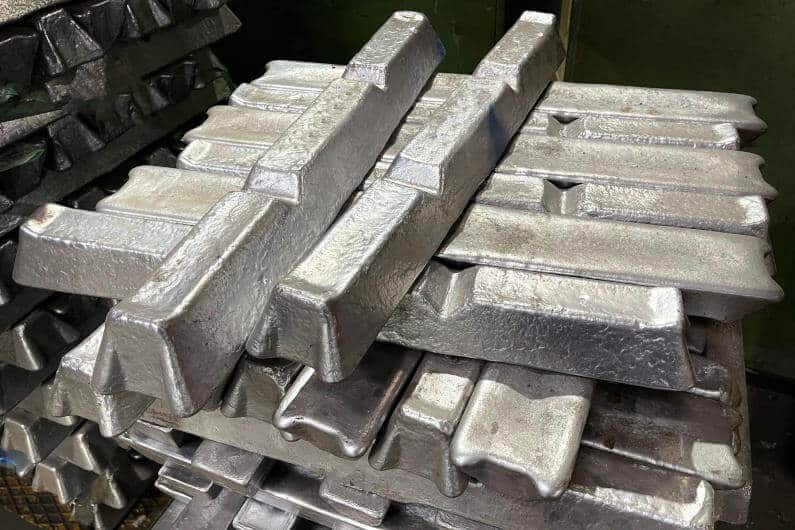
The primary thermal conductivity, tensile stamina, yield stamina, and elongation vary. Amongst the above alloys, A356 has the highest possible thermal conductivity, and A380 and ADC12 have the cheapest.
Alcast Company for Dummies

In accuracy spreading, 6063 is fit for applications where intricate geometries and top quality surface coatings are extremely important. Instances consist of telecommunication units, where the alloy's superior formability permits for streamlined and aesthetically pleasing designs while preserving structural honesty. Similarly, in the Lights Solutions sector, precision-cast 6063 elements produce stylish and effective illumination components that require intricate forms and good thermal performance.
It causes a better surface finish and far better rust resistance in A360. The A360 shows premium elongation, making it optimal for complex and thin-walled elements. In accuracy casting applications, A360 is fit for sectors such as Consumer Electronics, Telecommunication, and Power Devices. Its enhanced fluidity permits elaborate, high-precision parts like smartphone casings and interaction tool real estates.
Some Known Incorrect Statements About Alcast Company
Its distinct residential properties make A360 a beneficial choice for precision casting in these industries, enhancing item longevity and top quality. Aluminum alloy 380, or A380, is an extensively used casting alloy with numerous distinctive qualities. It uses outstanding castability, making it an optimal choice for accuracy spreading. A380 shows excellent fluidity when molten, guaranteeing intricate and thorough molds are precisely reproduced.
In accuracy spreading, light weight aluminum 413 radiates in the Consumer Electronics and Power Devices sectors. This alloy's remarkable corrosion resistance makes it an exceptional choice for outdoor applications, making certain lasting, resilient items in the pointed out industries.
More About Alcast Company
When you have actually made a decision that the aluminum pass away casting procedure is ideal for your job, a critical following step is choosing on one of the most suitable alloy. The aluminum alloy you choose will significantly influence both the spreading process and the buildings of the final product. As a result of this, you should make your choice meticulously and take an informed strategy.
Determining the most appropriate aluminum alloy for your application will suggest considering a large array of features. The first category addresses alloy attributes that affect the production procedure.
8 Easy Facts About Alcast Company Described
The alloy you choose for die casting directly impacts several facets of the spreading procedure, like just how easy the alloy is to collaborate with and if it is susceptible to casting flaws. Hot splitting, also known as solidification fracturing, is a common die casting issue for light weight aluminum alloys that can result in inner or surface-level rips or fractures.
Certain light weight aluminum alloys are a lot more at risk to hot cracking than others, and your option should consider this. An additional common defect discovered in the die spreading of light weight aluminum is pass away soldering, which is when the cast sticks to the die walls and makes ejection challenging. It can harm both the cast and the die, so you ought to look for alloys with high anti-soldering properties.
Rust resistance, which is already a noteworthy characteristic of light weight aluminum, can differ substantially from find more information alloy to alloy and is an essential characteristic to think about depending on the environmental conditions your product will be subjected to (Aluminum Casting). Use resistance is another residential or commercial property frequently sought in aluminum items and can separate some alloys
Report this page